Thermosets vs. Thermoplastics
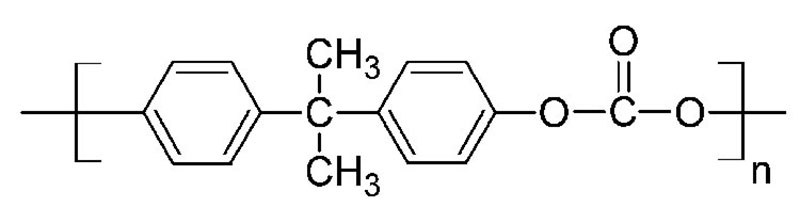
<p>A common question we get asked from time to time is, “What is the difference between a thermoset and a thermoplastic?” Here is a brief description to illustrate the distinction between the 2 categories of engineering plastic materials. A clearer understanding of why plastic materials react the way they do will help you make an informed decision as to what category of plastics is ideal for your application.</p><p>In a nutshell, the main difference between a Thermoplastic and a Thermoset is whether or not it can be melted down and recycled. A general rule of thumb is that Thermoplastics can be heated up to a certain temperature, depending on the material’s glass transition point, and can then be melted down for recycling or perhaps extrusion or injected into a mold for injection molding. As thermoplastics cool, they begin to harden into the desired shape without any chemical curing being performed to increase the strength of the material. Once a thermoplastic has cooled, it can now be machined or fabricated using common machining methodologies.</p><p>Thermosets on the other hand are cured and hardened into a specific shape, generally through the application of heat and pressure. Curing thermosets, (also known as vulcanizing), is an irreversible chemical process whereby the polymers in the material create permanent connections called “crosslinks” with the materials molecular chains. The crosslinking that occurs in a thermoset creates a very rigid material when cured. Once cured, thermosets are unable to be reprocessed or melted for reusability. While both materials exhibit their own beneficial characteristics, thermosets exhibit several advantages over thermoplastics including mechanical properties, thermal stability, as well as overall durability.</p>